Cylinders and Related Components
ACI is a leader in custom cylinder design and manufacture including the use of stainless and other exotic materials. Look to ACI to deliver functional equivalents of OEM cylinders and to develop innovative new designs using new technologies.
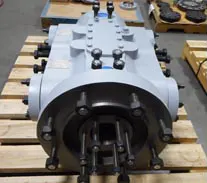
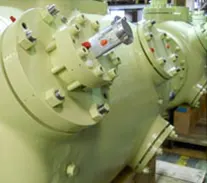
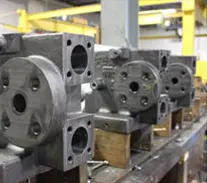
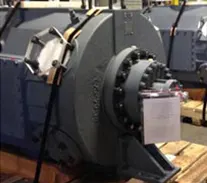
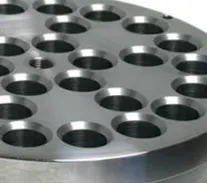
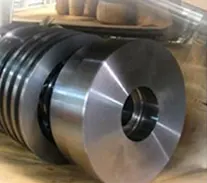
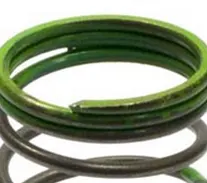
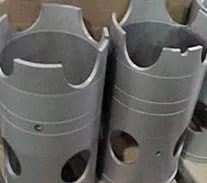
Learn About our Custom Compressor Solutions
ACI can build cylinders to your specifications or to match OEM specs and the new cylinder body can often utilize existing valves, piston and rod assembly, packing case. The new cylinders maintain the same centerline dimensions as the existing cylinder which allows the existing bottles to be reused and minimizes the capital cost to install new cylinders.
Replacement pistons and rods are available in numerous sizes, configurations and materials. Replacement components can generally be categorized as replications or performance enhanced. Replicated components simply clone the original design, thus offering no design upgrade. Performance enhanced components provide redesigned concepts that optimize maintenance ease, service life and safety.
Each of the four main types of poppet valves is suited to a particular application scenario.
Single Deck Valves
Single deck valves have only one layer of poppets, rings, or plates. They are used in compressors where it is necessary to keep the fixed clearance low. This is usually the case with high speed compressors, and some low speed compressors.
Generally if the pressure ratio is over 2, it is highly likely that most of the valves will be single decks.
These have less flow area than double deck valves or deck and a half valves which will result in taking more energy to push the gas through the valves.
Deck and a Half Valves
These valves have two layers of poppets, rings, channels, strips, or plates. These are usually used in low pressure ratio applications such as transmission of natural gas.
These valves have more flow area than single deck valves and require considerably less energy to push the gas through the valves.
These valves typically have slightly less fixed clearance than double deck valves.
Double Deck Valves
Double deck valves have two layers or levels of poppets, rings, channels, strips, or plates. These may be used in applications such as transmission of natural gas where the compressors operate at rather low pressure radios (usually less than 1.5)
They typically have more flow area than single deck valves, which results in lower energy required to push the gas through the valve.
If compressors are overloaded a lot of the time, changing from single deck valves to double deck valves may help to unload the compressor by adding to fixed clearance and by improving the efficiency of the compressor.
These valves have quite a lot of fixed clearance and are therefore not used in applications with pressure ratios over about 2.0, unless they are needed to allow gas to flow into and out of valve cap clearance pockets
Radial Valves
Radial valves made by ACI Services, Inc. have the most flow area of any available valve.
Typically these have 2 to 2 1/2 times the flow area of single deck valves.
These have poppets that are arranged to seat on a cylindrical surface. Radial suction valves have the poppets seat on the inside of a sleeve, and radial discharge valves have the poppets seat on the outside of a sleeve.
The fixed clearance associated with radial valves is comparable to that in double deck valves.
These extremely efficient valves manufactured by ACI Services, Inc. are justified in cases where the cylinders have limited valve area available and may result in reducing the energy required to push the gas through the valves by 50% or more.
A large number of rod failures are the result of inaccurate pre-stressing. ACI’s ExactoTorque is the patented solution. It can be used for a wide variety of mounting and industrial attachments (flange bolting, foundation bolting, etc.), especially where precise alignment and space restrictions are a concern.